中国钢铁业要实现从大到强的转变,绝不能错过智能制造这个机遇期。智能制造表面是技术问题,本质是经济问题,体现在信息通信技术的应用,关键却在业务与商业模式的创新、组织流程改革和企业文化的转变。本文针对这一热点,分析了智能制造的概念及其本质,并运用工业4.0的概念分析了钢铁行业推进智能制造的现状、价值、阻力和思路。
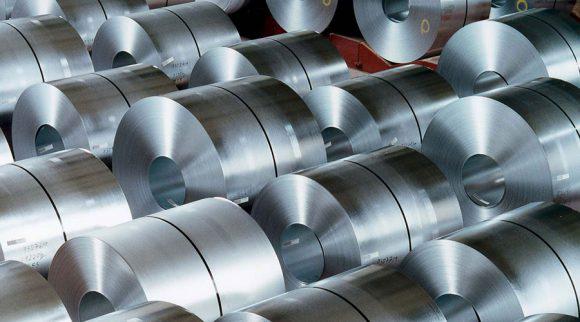
殷瑞钰院士曾经指出:钢铁行业未来的战略方向应该是智能化和绿色化。中国钢铁业要实现从大到强的转变,绝不能错过智能制造这个机遇期。但是,自从智能制造成为热点以来,争论就不绝于耳。如果没想明白而盲目冒进,就可能误入歧途,历史的机遇就可能丧失。笔者认为:智能制造的表面是技术问题,本质是经济问题;体现在信息通信技术的应用,关键却在业务与商业模式的创新、组织流程改革和企业文化的转变。
1、正路和歧途
著名经济学家熊彼特认为,创新的成功是用经济成功来衡量的。所以,智能制造的“误入歧途”就是采用了先进的技术却没有创造出应有的价值。大家的担心,就是因为看不到技术的价值体现。
误入歧途,不是技术本身的问题,而是没把技术用到能创造价值的地方。“从痛点出发”是企业技术创新常用的一种工作方法。然而,痛点往往都是老问题,而且过去解决不了的问题,现在仍然难解决。
为什么会出现这样的情况?有个寓言说得很形象:有人丢了钥匙,在路灯下面反复寻找。有人问:你肯定钥匙丢在这里吗? 那人说:“不肯定,但只有这里有光”。智能制造的误入歧途,也是这个道理。
智能制造的本质是加强协同能力,通过系统的力量创造价值。智能制造的价值点,常常不在某个部门的内部;通过知识的积累,让过去由人来创造价值的智能工作,让机器自动去做。所以,智能制造是靠系统创造价值、通过长时间积累创造价值。如果眼光习惯性地局限于部门内部、局限于眼前,往往只能看到价值不大的残羹冷炙,从而进入 “路灯底下找钥匙”的困局。
这种困局其实是经验主义作祟。毋庸置疑,中国钢铁行业在过去几十年取得了很大的成就。但是,这些成就往往是跟随、模仿、持续改进。而智能制造是转型、真正的创新。“病变而药不变,向之寿民,今为殇子矣”,经验主义会在无形中害人。
2、智能与知识管理
古人云:名不正则言不顺,言不顺则事不成。要理解智能制造,必须从正名开始,避免望文生义。
很多人把“智能制造”与“人工智能”混为一谈。两个概念相关,但侧重点却有所不同。在智能制造的语境中,“智能”强调的是信息的感知、决策和执行的整个过程,可以让主体适应环境并促进多个主体之间的协同。这一思想,可以追溯到维纳在20世纪40年代写的《控制论》(Cybernetics)。我们知道,工业4.0强调CPS(Cyber Physical System),而Cyber就源于Cybernetics。
而传统人工智能主要关注决策中的算法。我们看到:智能软件“阿尔法狗”的决策能力强到可以打败韩国职业棋手李世石;智能机器人却难以通过自主的协同完成除草、洗碗等简单的家务劳动。这就是决策和执行的差异。智能制造关注的是“知行合一”、感知就是为了执行。
为了实现智能制造的目标,就要搞清楚两类问题:要感知什么、如何决策。其实,在MES、ERP等传统信息系统中也要解决这两类问题。在钢铁行业,这两类问题的答案体现在各种标准中,如产品标准、工艺标准、操作标准等。这些标准明确了操作端收到什么信息、如何执行。这些标准是与产品和生产相关的、企业的核心知识。宝钢信息技术奠基人何麟生先生就自称是宝钢的“首席知识官”。
在智能制造时代,要管理的知识仍然是与产品和生产相关的、企业的核心知识,但针对的问题有所不同。在笔者看来,智能制造对应的知识,几乎都可以看成是对已有“标准知识”的修订或拓展。例如,新产品开发需要设计新标准、新用户来了要选择标准、标准要不断优化、生产参数超出标准要及时处理、产品的使用方法可以标准化等。这些知识过去是存在于专家的脑子中。在智能制造时代,则需要将它们显性化、规范化,最好能变成程序或标准的数据结构,以便于协同甚至被计算机直接应用。所以,“知识管理”是智能制造的重要内容。
3、对智能制造的认识
智能制造一般被翻译成Smart Manufacture,Smart含有灵活、敏捷、聪明的意味。事实上,智能制造确实能加快反应速度。典型的例子是通过数字化设计提升协同能力,缩短产品研发周期。在互联网时代,小众市场的需求进一步释放,新产品设计的需求增大,这对新产品设备速度提出更高的要求。这种要求传导到制造环节,会进一步影响到供应链和物流管理。这就为智能制造的广泛应用创造了机会。
“萝卜快了不洗泥”。如果产品研发到投产周期太短、投产批量太小,会产生大量负面问题,如质量不稳定、成本过高、能耗大等。所以,智能制造不仅要解决如何“更快”的问题,更要解决“更快”的负面问题。我们知道,用户的需求是对质量、价格和交货期三项因素的综合,“快”必须以质量和成本为基础,不可能“一快遮百丑”。
还有一种误区是把智能制造与“代替人”混为一谈。二者确实有关联。但智能制造的首要目的是克服人的缺点:反应速度慢、容易犯错、规范性差等;减少人也是重要的目标,但在智能制造的理论体系中是次要的。
智能制造是由ICT技术的发展引发的。借助ICT技术,拉近企业与客户、部门与部门、人和设备的距离,有助于人与人、人与机器、机器与机器更有效地协同、减少不必要的时间拖延;还可实现知识的共享、避免重复开发。这种逻辑不仅适合产品开发和生产,还可用于智能产品、智能服务。它们的本质都是通过网络实现协同和共享,以提升反应效率。如果从技术层面总结智能制造的共性,就是广泛深入地采用数字化和网络化手段。
4、工业4.0的本质
工业4.0是智能制造范畴内的一种体系。多数情况下,工业4.0就是在流水线生产个性化定制产品,将流水线的高效率和定制的灵活性结合起来。
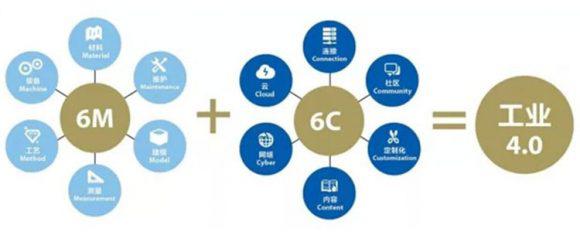
然而,仅仅是高效率和灵活性的结合,并不能保证生产的经济性。要保证经济性,本质上还是要看成本、质量和交货期。
有人认为:工业4.0发展到一定程度,必然取代工业1.0-3.0。但笔者认为:工业4.0的生产方式只是工业发展到一定程度的典型标志,不是意味着所有企业都采用工业4.0推崇的生产方式。这就好比:人类的出现是生物进化到一定程度的标志,但并不意味着所有的动物都会进化到人。
这个观点可以被历史所印证。我们知道,现代西方发达国家处于工业3.0阶段,但他们的制造业也不都是用自动化流水线生产的。很多科研设备、高档奢侈品要靠手工。由此可见,工业3.0也没有淘汰掉其他的生产方式。
工业4.0属于先进的生产方式,但其他的生产方式未必落后。例如,飞船不是在流水线上生产的,其生产方式应该属于工业1.0。但这丝毫无损于其高大上的技术地位。而且,工业1.0的行业也可以搞智能制造:全数字化设计的火箭,就是智能制造。
我们预计工业1.0-4.0会因各自的优点而长期共存。例如:特殊试验设备是个性化强的单件产品,没必要开发流水线,就会停留在工业1.0;手机等快消品的更新换代速度很快,自动化流水线的建设速度难以与需求匹配,更适合停留在工业2.0。工业3.0具有高效率、高质量、低成本的优点,特别适合个性化需求不强的石油化工等大型流程行业。由此可见,应该采用何种生产方式,取决于生产方式的经济性。
有人认为:工业4.0是工业3.0发展成熟之后的结果,这种观点其实也是片面的。红领制衣就是在人工流水线上从事个性化定制,从工业2.0直接进军工业4.0。在笔者看来,工业3.0的终极目标是全自动化的无人工厂,而工业4.0不必在这个基础上产生。提高流水线的自动化水平(工业3.0)与推进个性化定制(工业4.0)完全可以同步发展。
工业4.0主要是解决在流水线上经济地生产个性化定制的问题。为此需要解决两类问题:首先是让流水线具备个性化生产的能力;其次是降低个性化生产的负面作用,以便具有更好的经济性。特别地,第一个问题解决后,主要矛盾就转移到第二个问题——笔者将这些问题的阶段称为“工业3.5后”。我们注意到:这类问题也是精益生产关注的问题。有人说:智能制造是精益生产的延伸、精益生产是智能制造的基础,是有一定道理的。
个性化定制生产肯定会产生负面影响,在产品质量、成本、效率、能耗、交货期等方面,大规模生产一定是有优势的。而工业4.0的大量技术就是用来减少这些负面影响。工业4.0强调的质量、成本、能耗和交货期,往往是用来弥补这些弱点和不足的。当定制化生产的副作用小到一定程度、定制化生产所带来的效益就能推动工业4.0走向经济的成功。所以,“工业3.5后”决定工业4.0的经济性。
5、从概念本质看钢铁行业现状
特钢生产的流水线特征往往不明显,所以特钢的生产应该属于工业1.0-2.0。螺纹钢的生产一般是标准化的,所以更适合停留在工业3.0。而生产板材的先进钢铁企业早在20多年前就实现了“按订单组织生产”、“标准+ɑ”,具备了工业4.0的基本特征。事实上,工业4.0提到的CPS、ERP、MES、PLM、信息集成等技术,在宝钢的计算系统里面都可以找到原型,只是当初的叫法不同。所以,宝钢老领导何麟生先生认为宝钢目前至少处于工业3.5的水平。
工业4.0先进的实践往往发生在应用价值大而技术难度相对较低的地方。钢铁行业就具备这样的特点:部分用户对定制的需求强烈,而产品的物料跟踪却相对简单。
钢铁行业有非常先进的一面,也有“相对落后”的一面。要用智能制造提升钢铁行业的技术水平,还是应该从痛点出发。在笔者看来,钢铁行业至少有如下几个痛点:
第一,钢铁生产线并非理想的流水线。殷瑞钰院士把钢铁生产体系看作“耗散系统”,能量总是要损失的。这决定了钢铁生产几乎永远不会是理想的流水线。“耗散系统”的本质无法改变,但我们可以做得更好、可以用智能化带动绿色生产。这类问题可以归结到改进工业2.0的先天不足。
第二,钢铁企业的自动化水平仍然有待提高。即便是宝钢,也是在工业3.0并不完美的时候推进工业4.0的。浦项将智能工厂的终极目标确定为“无人值守”,本质上就是要提升自动化的水平。这类问题可以归结为工业3.0的问题。
第三,定制化生产的负面作用严重。连铸交接坯浪费、质量余材多、产品质量不稳定、交货期长等现象,本质上都是定制化生产带来的负面问题。在钢铁行业毛利很低的情况下,应该更加重视这方面的问题。笔者将这类问题称为“工业3.5后”的问题。
第四,服务的问题。在定制化生产时,用户遇到的很多问题与设计和服务有关。按照目前的观点,造成这种现象的本质是缺乏优秀的专家。而且由于优秀专家总是“稀缺资源”,钢铁厂的服务很难面对中小客户。笔者认为,随着“供给侧改革”的发展,下游中小企业的质量意识和自动化水平会逐步提高,对服务的要求肯定会大大加强。通过推进“智能服务”,提高专家工作效率,是解决这个问题的方法之一。
6、推动智能制造的价值与阻力
钢铁行业推进智能制造面临诸多尴尬的困境:要推进工业4.0,却发现自己并不落后;现实中有很多痛点,却往往是长期无法解决的老大难问题。要破解这些难题,需要具体问题具体分析。
在笔者看来,造成能耗高、自动化水平低等现象的首要原因是经济问题。随着我国对环境的要求越来越严格、劳动力成本越来越高,解决和改善这些问题的难度会逐步变小、动力会逐渐增大。但是,解决这些问题应该与智能制造思想相结合,以提高技术经济性。事实上,在个性化定制的前提下推进操作、计划调度的无人化,都可看作是智能制造的范畴。
后面两个问题也可通过智能制造的思路来解决。具体地说,就是通过加强信息感知和知识管理,解决个性化定制的负面问题并加强个性化服务。其实,人们很早就意识到这两类问题,只是苦于“无计可施”。其中,最缺乏的知识是对产品“适用性”的研究不够。
从经济性上看,工业4.0既要实施个性化定制,又必须努力减少定制的负面影响。要解决这个问题,离散制造业常采用模块化方法,在钢铁行业则应该尽量提高钢种的通用性。否则,个性化需求越强,生产组织的难度就越大、浪费可能就越大、交货期就越长、质量稳定性就越难保证。
然而,钢铁企业的知识结构往往碎片化严重,难以支持上述设想。我们往往用专一而又严格的成分和工艺要求来对应特定用户。企业内部的产品标准常常是根据生产控制能力给出的、允许波动的范围很小。产品开发成功后,人们知道在成分工艺的狭小控制范围内能够满足用户需求,但并不一定清楚超出范围能否依然满足用户需求、更不清楚其他的成分体系能否满足用户需求。事实上,钢铁企业常常不太清楚用户的使用过程,也就根本无法回答上述问题。这种碎片化的知识结构很难支撑生产组织的改进,智能制造技术也是“巧妇难为无米之炊”。
企业为什么不重视这些知识的结构化呢?主要原因是动力不足、阻力过大。
第一,公司层面的动力就不足。智能制造可能带来的价值潜力是巨大,但是却很难被意识到——因为很多价值损失被“合理地”掩盖掉了。人们把成分工艺超标但适合用户需求的产品判为降级看作正常的;把多付出的合金和工艺成本看作正常的;把频繁的异钢种连浇看成正常的;把交货期长、库存大看成正常的;把操作或计划不合理看作正常的;把反复大生产试验看作正常的;把设备原材料成本高看作是正常的……其实,通过智能制造,这些地方都能创造价值。
第二,部门的动力不足。很多实际问题是要多个部门协同解决。但只要某个部门能够把问题推到其他部门头上,解决问题的动力就小了、难以形成合力。另外,很多人意识不到信息的集成能够给自己的业务带来好处。
第三,考核体制未必鼓励个人贡献知识。在很多企业,为便于考核,实际主要鼓励直接贡献、不鼓励间接贡献。解决实际发生的问题是直接贡献,而让问题不再发生就是间接贡献。所以,如果把知识贡献出来让机器完成,个人就丧失了创造价值的机会甚至工作岗位,这种现象与“带好徒弟、饿死师傅”的道理是一样的。
最后一点:不知道如何管理知识。很多企业的知识管理变成了对知识产权和论文资料的管理。如前所述,这些知识并非智能制造所关心的知识。要管好智能制造所需的知识,要在方法、组织和工具上有所创新。
7、推动智能制造的思路
智能制造首先遇到的可能是组织、评价和文化问题。这些问题解决以后,对知识的有效管理与使用等技术问题就会成为关键。笔者认为,下面三件事非常重要。
第一,用ICT技术推进透明化。透明化的目的是让价值损失显性化,从而便于智能制造的推进。智能制造是价值驱动的,但价值点往往是隐含的。透明化就是把价值点显现出来。未来的透明化,应该是对业务运行是否正常的评估,让质量下降、效率降低、过度研发、协同的失败等价值损失能够通过数字化的方法有效地展现出来、显性化,并在必要时推送给管理者。宝钢老领导何麟生先生很重视SCOR模型和设备生命周期管理,在他看来,就是要关注物料和备品备件的使用是否合理。对于透明化,很多人想到的是把大量数据直观地展示出来。但在笔者看来,这种原始的透明化很容易让人的关注力淹没在数据的海洋中而失焦,未必能带来价值。
第二,推动知识的积累。有了知识才能为推进智能制造奠定条件。如前所述,钢铁厂的知识过于“碎片化”,不适合智能制造的需求。为了解决这个问题,新产品研发和试制时,就应该考虑到与其他产品的互用问题、成分工艺超标时的处理方法;成分和工艺的开发经验应该尽量转化为数学模型;产品生命周期的相关数据和知识应该智能化地管起来;系统研究产品使用知识;生产管理和操作的模型化等。需要注意的是:这些改变需要有制度和流程上的配套。
第三,工业软件的支撑。智能制造的思想要落地,最终还是需要工业软件的支撑。在笔者看来,目前还没有特别适合的软件系统。钢铁行业或许可以做“第一个吃螃蟹的”。事实上,钢铁行业常常做“第一个吃螃蟹的”:中国最早的MES就是在宝钢投运的,钢铁行业也是最早在流水线上实现个性化定制的行业。如果钢铁行业能在智能制造时代领先,也未必是不可能的。
8、结束语
推进智能制造非常困难。为了避免误入歧途,必须要事先想清楚。但是,即便把问题想清楚了,困难也不会减少,而是会看到更多、更大、更本质的困难。要推进智能制造,就必须克服这些困难、不能绕着走。宝钢老专家王洪水先生认为:系统地结构化知识将是迎接智能制造时代的关键一步。笔者认同这个观点。